How Defoamers Improve Product Quality and Reduce Waste in Production
How Defoamers Improve Product Quality and Reduce Waste in Production
Blog Article
How Defoamers Improve Effectiveness in Production and Manufacturing

Recognizing Defoamers
Defoamers play a vital role in numerous making processes by properly combating the formation of foam, which can impact and interfere with operations product high quality. Foam can arise in many contexts, such as during mixing, home heating, or chain reactions, potentially causing inefficiencies and variances in products. The mechanism whereby defoamers run commonly involves decreasing the surface area tension of the fluid, permitting bubbles to coalesce and rise to the surface area more easily, where they can after that break.
Defoamers are developed from a range of chemical substances, including natural materials, silicones, and surfactants, each customized to particular applications and processes. The choice of defoamer depends on factors such as the kind of product being processed, temperature, and the presence of various other ingredients. Efficient defoamers not only decrease foam development however also maintain compatibility with the item, making certain that there are no negative impacts on the final result. Recognizing the residential or commercial properties and functions of defoamers is essential for suppliers intending to enhance their processes, boost efficiency, and maintain the honesty of their items.
Key Benefits of Defoamers
Using defoamers in manufacturing procedures uses a series of considerable advantages that boost operational effectiveness and item high quality. One of the key benefits is the reduction of foam development during manufacturing, which can block machinery and interrupt workflows. By minimizing foam, defoamers make sure smoother procedures, resulting in lowered downtime and maintenance expenses.
Additionally, defoamers enhance item uniformity by stopping air entrapment, which can compromise the stability of the end product. This is specifically crucial in sectors where visual look and texture are important, such as in paints, finishings, and foodstuff. Enhanced item high quality not just meets consumer expectations yet also enhances brand reputation.
Furthermore, defoamers can help in enhancing source usage. By enhancing the efficiency of resources utilization, they add to cost financial savings and reduced waste, lining up with sustainability objectives. The application of defoamers can lead to shorter handling times, making it possible for manufacturers to increase manufacturing ability without substantial funding financial investment.
Applications in Different Industries
In producing processes throughout numerous markets, the application of defoamers plays a critical duty in boosting effectiveness and product quality. These chemical additives are used in fields such as food and drink, drugs, and fabrics to alleviate foam-related difficulties.
In This Site the food and beverage industry, defoamers are essential during the fermentation procedure, preventing frothing that can interfere with manufacturing and ruin the product's navigate to this website integrity. Similarly, in the pharmaceutical field, defoamers are made use of in the formula of liquid medications, making sure uniformity and stability while reducing waste.
Textile manufacturing also takes advantage of defoamers, as they are utilized in dyeing and ending up processes to promote also distribution of chemicals and dyes. This application not only improves the last item's look yet likewise decreases the quantity of water and power consumed during manufacturing.
Furthermore, in the paper and pulp market, defoamers help preserve process efficiency by reducing foam that can prevent machinery performance. On the whole, the varied applications of defoamers across these markets underscore their importance in maximizing manufacturing processes and providing high-quality products.

Selecting the Right Defoamer
Choosing a proper defoamer is essential for maximizing efficiency and quality in manufacturing processes. The choice of defoamer depends on various variables, consisting of the details application, the kind of foam being produced, and the formula of the product being manufactured.
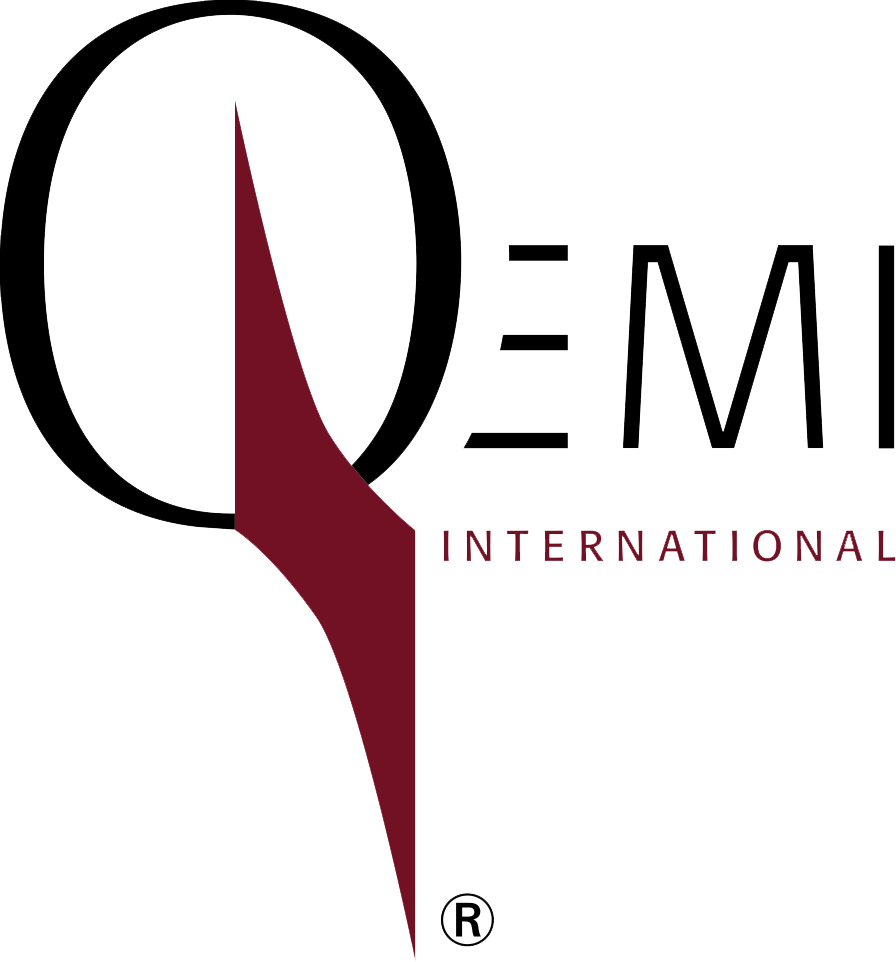
To start with, take into consideration the chemical compatibility of the defoamer with various other components in your formulation. A defoamer that interacts adversely with other components can adversely influence product quality. In addition, the temperature level and pH variety during handling are vital; some defoamers carry out optimally under particular problems while becoming inadequate in others.
Second of all, assess the defoamer's performance features, such as its capacity to rapidly reduce foam and its perseverance during manufacturing. It is important to select a product that not only eliminates foam swiftly however also maintains its effectiveness with time.
Last but not least, think about environmental and governing variables, especially official statement if your manufacturing procedure undergoes strict conformity requirements. Selecting a biodegradable or low-toxicity defoamer can aid satisfy sustainability objectives while ensuring functional effectiveness. By thoughtfully analyzing these requirements, suppliers can make informed choices that enhance efficiency and item integrity.
Finest Practices for Implementation
Effective execution of defoamers in manufacturing procedures calls for careful preparation and adherence to finest methods. Choosing the ideal defoamer, as previously talked about, is important; ensure it is compatible with the materials entailed and resolves the recognized lathering problems efficiently.
Next, keep clear interaction with all stakeholders, including operators and quality assurance groups. Educating sessions can assist guarantee that everyone recognizes the application procedures, potential effect on item high quality, and security considerations. Implementing a test stage can also be advantageous; display efficiency carefully to gauge performance and make needed adjustments.
In addition, routine testing and surveillance of foam degrees can offer valuable understandings into the defoamer's efficiency gradually. Adjusting does in action to changes in manufacturing variables will aid preserve optimal efficiency - defoamers. Lastly, documenting all procedures and results promotes continual enhancement, permitting fine-tuning of defoamer usage and enhancing total productivity in making operations.
Conclusion
In recap, defoamers play a critical role in improving effectiveness within production and manufacturing processes. By minimizing foam development and assisting in bubble coalescence, defoamers add to improved item quality, uniformity, and functional effectiveness.
The benefits prolong to product quality and cost savings, as defoamers help simplify procedures.Defoamers play an essential role in various making procedures by properly combating the development of foam, which can interfere with procedures and impact item high quality. Comprehending the properties and features of defoamers is necessary for makers aiming to optimize their procedures, boost efficiency, and preserve the integrity of their items.
Using defoamers in manufacturing procedures supplies a variety of considerable benefits that boost functional effectiveness and product top quality.In addition, defoamers enhance product uniformity by stopping air entrapment, which can jeopardize the integrity of the last item.
Report this page